ATEX Compliance Report
ATEX Compliance Report: What Is It?
In facilities where flammable chemicals can be released into the environment, such as production areas and storage areas, there are numerous electrical equipment regardless of the storage quantities. These equipment must be suitable for the hazardous areas where they are located in terms of their ex-proof properties. In addition to being suitable for ex-proof properties, it is also important for these properties to be maintained. Therefore, the equipment should be installed and maintained using wiring and piping components that are suitable for ex-proof properties.
ATEX Compliance Report: It is a document that certifies that the equipment used in facilities where explosive atmospheres are present or may be present is selected, installed, and maintained appropriately according to the explosive environments they are located in.
Why Should an ATEX Compliance Report be Prepared?
The compliance of ex-proof equipment used in the facility should be documented in the Explosion Protection Document (EPD), prepared or obtained by the employer, in accordance with the “Regulation on the Protection of Workers from the Hazards of Explosive Atmospheres“.
Regarding the compliance of ex-proof equipment, the following statement can be found in the “Regulation on the Protection of Workers from the Hazards of Explosive Atmospheres“:
ARTICLE 10 – (1) While fulfilling the obligation specified in Article 6, the employer prepares the Explosion Protection Document, which includes the issues mentioned in the second paragraph.
2) The Explosion Protection Document includes the following:
- Determination and evaluation of explosion risk,
- Measures to fulfill the obligations determined in this Regulation,
- Areas classified according to Annex-1 in the workplace,
- Places where the minimum requirements specified in Annex-2 and Annex-3 will be applied,
- Design, operation, control, and maintenance of the work equipment, including workplaces and warning devices, in compliance with the safety rules,
- Compliance of all equipment used in the workplace with the Regulation on Health and Safety Conditions for the Use of Work Equipment published in the Official Gazette dated 25/4/2013 and numbered 28628.
.
In addition, according to the “Regulation on Equipment and Protective Systems Intended for Use in Potentially Explosive Atmospheres“, in addition to being suitable for explosive atmospheres, equipment also needs to be appropriately marked.
Regarding the proper marking of ex-proof equipment, the following statements can be found in the “Regulation on Equipment and Protective Systems Intended for Use in Potentially Explosive Atmospheres
ARTICLE 18 – (1) The CE mark shall be affixed to the product or its information plate in a visible, legible, and indelible manner. If this is not possible or cannot be guaranteed due to the nature of the product, it shall be affixed to the packaging and accompanying documents.
(2) The CE mark shall be affixed before the product is placed on the market.
(3) The CE mark shall be followed by the identification registration number of the notified body involved in the manufacturing control phase. The identification registration number of the notified body shall be affixed by the organization itself or by the manufacturer or authorized representative upon its instruction.
(4) The CE mark and, where applicable, the identification registration number of the notified body shall be followed by the special marking for protection against explosion, the symbols for equipment-group and category, and, where applicable, the information and other markings specified in Article 1.0.5 of Annex-2.
(5) The CE mark may be followed by other markings, symbols, and the information specified in the fourth paragraph, as well as any other marking indicating a specific risk or use. Products designed for specific explosive atmospheres must be properly marked.
(6) The Ministry shall rely on existing mechanisms to ensure the correct implementation of the legislation regulating the CE mark and take necessary measures in case of its inappropriate use.
How Is the Compliance of Ex-Proof Equipment Determined?
This is where the ATEX Compliance Report comes into play. he ATEX Compliance Report includes the control of ATEX compliance, identification of non-compliances, and necessary recommendations for rectifying non-compliances for each equipment present in explosive atmospheres as defined in the Explosion Protection Document (EPD).
How Is the Compliance Status and Non-Compliances of Ex-Proof Equipment Determined?
There can be non-compliances in various aspects of ex-proof equipment, such as protection level, equipment group, temperature class, electrical and grounding installations, and equipment sealing. These non-compliances prevent the equipment from having adequate protection level. These non-compliances can occur due to various factors such as equipment selection, installation, or maintenance.
There are three types of inspection levels according to the TS EN 60079-17 Standard for evaluating compliance in terms of installation, maintenance, or cabling. These levels are summarized as follows:
Visual Inspection: Inspection performed by visually examining the equipment without disassembling the enclosures or cutting off the power supply.
Close Inspection: Inspection conducted when a closer examination of the equipment is required, where the inspector reaches the equipment using ladders, compared to the visual inspection.
Detailed Inspection: In addition to the close inspection, inspection where enclosures are opened or test equipment is used to identify defects.
Among the three types of inspections, Visual Inspection is the most effective type of inspection as it can be easily repeated periodically and can identify deficiencies to a large extent. Visual inspection is based on visually examining the equipment according to 25 questions defined in the TS EN 60079-17 standard to identify and rectify deficiencies.
In the Visual Inspection conducted by ProSCon Engineering, the equipment is photographed, visually examined according to the 25 questions, and deficiencies and non-compliances are noted. Later, these non-compliances are compiled into a table along with recommendations for rectification and presented to the facility authorities.
The non-compliances identified in the visual inspection are reported by referring to relevant standards and citing national and international sources. For example, if a non-compliance is identified in an “d” type of protection in a “flame-proof” equipment, a recommendation is made in accordance with the TS EN 60079-1 Standard, or for grounding installations, a recommendation is made according to the TS EN 60079-14 Standard.
What Does Visual Inspection Include?
The purpose of the visual equipment inspection conducted by ProSCon Engineering is to identify non-compliances (such as ex-proof properties of equipment, ex-proof equipment labels, suitability of electrical installations used, and non-compliance with the explosive atmosphere where the equipment is located) that can be observed externally without disassembling the equipment or cutting off the power supply. The visual equipment inspection is completed through the following stages, and the situations encountered are documented by photographing them in a clear manner, item by item.
The first stage of the equipment compliance report is to compile a list of equipment located in hazardous areas. This is to ensure that no equipment is overlooked during the inspection. The aim is to ensure that no equipment is overlooked during the inspection process.
All electrical equipment, whether ex-proof or not, located in hazardous areas can pose a ignition source hazard. All electrical equipment in hazardous areas should be individually examined and noted, and the adequacy of their ex-proof properties should be evaluated.
The most important factor in equipment examination is the adequacy of the ex-proof features stated in the certificate and the markings on the ex-proof equipment labels. If these properties are not suitable for the hazardous areas they are located in, they should be marked as critical non-compliances, and immediate changes and corrections should be made in this regard.
Having ex-proof properties alone is not sufficient for equipment compliance. Electrical installations (cables, junction boxes, conduits, etc.) providing power to the equipment should also have specific characteristics based on the protection types and their locations. Electrical installations can lose their suitable properties due to damage during installation or over time.
The non-compliances in equipment can vary depending on the type of equipment and ex-proof properties. Non-compliances should be rectified by individuals trained in ex-proof equipment and capable of maintaining the ex-proof properties of the equipment.
The photographed non-compliances are explained to the authorities, indicating their location on the equipment and the cause, along with recommendations for rectification. The most suitable solution methods for the facility are determined by ProSCon Engineering employees for each type of non-compliance category, along with appropriate solution recommendations. In addition, the integration of the ATEX process with the Change Management System is ensured to maintain ATEX compliance in the facility for extended periods.
How Often Should Periodic Ex-Proof Equipment Inspections Be Repeated?
Non-compliances can occur in equipment due to wear, malfunctions, and maintenance resulting from these malfunctions. Therefore, according to the TS EN 60079-17 Standard, inspections should be repeated at intervals determined according to the type of equipment, unless an expert opinion states otherwise, with a maximum interval of 3 years.
All ex-proof equipment used in the workplace should undergo inspections and their compliance should be verified in accordance with the “Regulation on Health and Safety Conditions for the Use of Work Equipment“.
Equipment Used in Explosive Atmospheres
ARTICLE 7/A – (Additional: RG-18/2/2022-31754)
(1) The periodic control of equipment and protective systems intended for use in potentially explosive atmospheres, which fall under the scope of the Regulation on Equipment and Protective Systems Intended for Use in Potentially Explosive Atmospheres (2014/34/EU) published in the Official Gazette dated 30/6/2016 and numbered 29758, also includes the verification of compliance with the said Regulation in addition to inspections and tests.
(2) The verification of compliance with equipment used in explosive atmospheres is carried out at intervals determined according to the type of equipment, including the initial installation of the equipment. During the verification of compliance with equipment used in explosive atmospheres, the continuation of the characteristics covered by the conformity certificate is ensured in accordance with the TS EN 60079 and TS EN ISO 80079 series.
Findings and Recommendations in ATEX Compliance Report
ATEX compliance studies are carried out using the ExA inspection developed by ProSCon. ExA inspection is an inspection and ex-equipment asset management software integrated with tablets and web platforms.
All equipment present in explosive atmospheres in the facility is evaluated, and the identified non-compliances are categorized into four different categories:
- Critical Non-Compliance: These non-compliances pose a significant risk to working conditions and need to be rectified urgently.
- Major Non-Compliance: These non-compliances pose a risk to working conditions, but their urgency is not as high as critical non-compliances. These non-compliances can turn into critical non-compliances if improvement actions are not taken after a while.
- Minor Non-Compliance: These non-compliances do not pose as significant risks as critical and major non-compliances, but they can turn into critical or major non-compliances if improvement actions are not taken after a while.
- Recommendation: These non-compliances do not require mandatory improvement actions to a large extent. However, they are recommendations that would be beneficial for the working environment and equipment health.
ProSCon Engineering employees provide suitable solution recommendations for each type of non-compliance category to the facilities, aiming to determine the most effective solution methods for the facility. In addition to these solution recommendations, the integration of the ATEX process with the Change Management System is ensured to maintain ATEX compliance in the facility over extended periods.
If you would like to review the technical articles published about ATEX Compliance Report, you can use the links below.
- The Importance of Visual Inspection in Hazardous Areas
- Dust Explosions
- Control and Crisis Management of Flammable/Explosive Atmospheres in Industrial Facilities
For our trainings in compliance with ATEX Compliance and IECEx competence scheme for initial, visual, and sample inspections of Ex-proof equipment, you can use the links below.
Our Services
Our Trainings

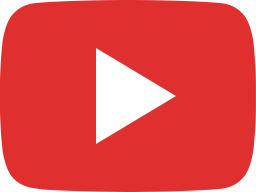
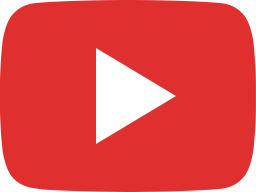
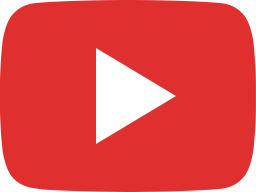

Key Words:
ATEX Compliance Report, ATEX, TS EN, Standards, ATEX Compliance, Ex Equipment, Inspection, Maintenance, TS EN ISO, Hazard, Dust, Explosion, Industrial, ATEX Process, Ex-proof Equipment Inspection, TS EN Standards.