Explosion Protection Document | EPD
What is Explosion Protection Document (EPD)
According to the “Regulation on the Protection of Workers from Hazards of Explosive Atmospheres,” the Explosion Protection Document (EPD) is defined as a document prepared to protect the health and safety of employees from the hazards of potential explosive atmospheres that may occur in workplaces.
For a more detailed description and explanation:
The Explosion Protection Document is a document that determines the type and extent of hazardous areas caused by gas/vapor or dust chemicals that may occur during normal operating conditions or expected abnormal situations in factories or facilities. It includes drawings illustrating these areas and provides recommendations for making them safe.
Why Should the Explosion Protection Document (EPD) be Prepared?
The “Regulation on the Protection of Workers from the Hazards of Explosive Atmospheres” assigns several responsibilities to the employer regarding explosion prevention and protection.
Article 5 – (1) The employer takes measures appropriate to the nature of the operations to prevent explosions and ensure protection from them. These measures comply with the following basic principles and priority order:
- Preventing the formation of explosive atmospheres,
- If it is not possible to prevent the formation of explosive atmospheres due to the nature of the operations, preventing their ignition,
- Taking measures to reduce the harmful effects of explosions to the health and safety of employees.
(2) The measures specified in the first paragraph are taken together with measures to prevent the spread of explosions if necessary. These measures are reviewed at regular intervals and after significant changes in the workplace.
Why and How Often Should the Explosion Protection Document (EPD) be Revised?
Changes in chemicals, processes, or equipment can lead to changes in hazardous areas. These changes may require the review and revision of the Explosion Protection Document.
For example:
- The emergence of new sources of release after a change in the process,
- Change in the chemical or process resulting in the chemical becoming flammable,
- Changes in process pressure,
- Changes in operational steps leading to new sources of release,
- Changes in ventilation conditions used in hazardous areas,
- Changes in equipment and instruments used within hazardous areas as part of process improvement or revision.
The Explosion Protection Document should be revised to reflect these changes. Additionally, the Explosion Protection Document (EPD) should be reviewed and revised after changes in standards. When examining examples of good practices from international organizations, it is observed that review and revision activities are conducted every five years without any changes.
The Explosion Protection Document prepared by Proscon Engineering not only ensures the implementation of the required measures by the employer but also provides the necessary methods to ensure the continuity of these measures to businesses.
What are the Minimum Information Required in the Explosion Protection Document?
The “Regulation on the Protection of Workers from the Hazards of Explosive Atmospheres” specifies the minimum information that should be included in the Explosion Protection Document (EPD) in the following article:
Article 10 – (1) When fulfilling the obligation stated in the 6th article, the employer prepares the Explosion Protection Document that includes the matters specified in the second paragraph.
2) The Explosion Protection Document includes the following:
a) Identification and evaluation of explosion risk,
b) Measures to fulfill the obligations specified in this Regulation,
c) Areas classified according to Annex-1 in the workplace,
d) Places where the minimum requirements specified in Annex-2 and Annex-3 will be applied,
e) Written confirmation that the design, operation, control, and maintenance of work equipment, including workplaces and warning devices,
comply with the safety rules published in the Official Gazette dated 25/4/2013 and numbered 28628, which regulates the Health and Safety Conditions for the Use of Work Equipment.
.
The steps followed in assessing the explosion risk and preparing the Explosion Protection Document (EPD) according to TS EN 60079-10-1, TS EN 60079-2, and TS EN 16985 standards are as follows:
- Identification of chemicals that may create an explosive atmosphere,
- Determination of leakage points (release sources) of evaluated chemicals,
- Determination of potential explosive atmospheres (zones) based on release sources,
- Modeling of zone maps with sample drawings and layout drawings,
- Determination of minimum ex-proof specifications required for equipment to be used in identified zones,
- Identification of ignition sources in designated zones and determination of necessary measures to eliminate hazards,
- Creation of an explosion impact table for possible explosion scenarios.
- General findings and identification of deficiencies observed in the facility.
Assessment of Ignition Source Risks
Facilities where hazardous chemicals are stored and produced are generally established and operated according to certain codes and standards. These standards include best practice examples to ensure the absence of ignition sources in these areas resulting from hazardous area assessments. The main standards used in industrial facilities include NFPA (National Fire Protection Association), BS (British Standards), and API (American Petroleum Institute) standards.
These standards used in hazardous area classification studies also include parameters related to the characteristics and persistence of potential flammable atmospheres. The equipment used within the designated areas must comply with the designated classes in the standards. Furthermore, for tasks to be carried out in hazardous areas such as hot work and maintenance, work permits are applied to ensure that factors such as hot surfaces and sparks, which can create ignition sources, are not present in the presence of a flammable atmosphere. In this regard, such work is strictly prohibited in areas with continuous release sources, while work permits are used to enable work in areas where the main release source is present when there is no hazardous area.
The designed and operated processes should be designed to prevent leaks and spills of hazardous chemicals, and the systems applied in the operating process should include control of ignition sources. The following practices can be given as examples for controlling unwanted ignition sources:
- lectrical area classification,
- Control of personal ignition sources,
- Work permits,
- Control of static electricity and leakage currents.
According to the ranking study conducted by Rew and Spencer in 1997, which is included in the “Development of a method for the determination of on-site ignition probabilities” published by HSE, the ignition potentials are given in the table below:
Category | Ignition Source Sample | Ignition Potential |
Exact | Open flame, Ignition Burner | p = 1 |
Strong | Electric motor, Hot Work | p > 0.5 |
Medium | Vehicles, Faulty cables | 0.5 > p > 0.05 |
Weak | Mechanical Sparks | p < 0.05 |
Negligible | Radio Frequency Sources, Intrinsically Safe Equipment | p = 0 |
Is the Proper Preparation of the Explosion Protection Document Sufficient to Avoid Hazards in Hazardous Areas?
In facilities where flammable chemicals are stored, used, and produced, the correct preparation of the explosion protection document alone is not sufficient. After correctly identifying the hazardous area:
- The suitability of the equipment used within the hazardous area,
- Proper installation and assembly of suitable equipment according to standards,
- Maintenance carried out by trained personnel following the standards for properly installed and assembled equipment
is required.
Equipment Selection for Hazardous Areas
The most important reason for preparing the explosion protection document is to achieve the optimum level of protection. This document prevents unnecessary expenses by using equipment and apparatus with higher safety features than necessary, and ensures that employees and the facility do not become unsafe in terms of explosions due to the use of equipment and apparatus with inadequate safety features. The maximum level of protection that can be achieved within the scope of ATEX
There are three main characteristics to consider in equipment selection:
- Zone type
- Equipment group
- Temperature class
Zone types are divided into three categories based on the frequency and continuity of the zones where the equipment is located:
- Zone 0/Zone 20 – 1G/1D
- Zone 1/Zone 21 – 2G/2D
- Zone 2/Zone 22 – 3G/3D
Table of explosion protection zones within the scope of ATEX Equipment groups are divided into three categories based on the type of chemicals that cause the formation of the hazardous area:
- IIA – Generally hydrocarbon derivatives
- IIB – Most alcohols and some hydrocarbons
- IIC – Hydrogen, acetylene, carbonyl sulfide
Temperature classes are divided into six categories based on the self-ignition temperatures of the chemicals that cause the formation of the hazardous area:
- T1 -<<450°C
- T2 -<<300°C
- T3 -<<200°C
- T4 -<<135°C
- T5 -<<100°C
- T6 -<<85°C
Evaluation of the Explosion Risk
The purpose of the Explosion Protection Document is to assess the possible explosion risks and prevent these risks. Article 6 of the “Regulation on the Protection of Workers from the Hazards of Explosive Atmospheres” explains the evaluation of explosion risks as follows:
Article 6 – (1) When carrying out risk assessment studies in accordance with the “Occupational Health and Safety Risk Assessment Regulation” published in the Official Gazette dated 29/12/2012 and numbered 28512, the employer also takes into account the following issues in the assessment of specific risks arising from explosive atmospheres:
- a) The probability of the formation of an explosive atmosphere and its persistence,
- b) The probability of the presence, activation, and effectiveness of ignition sources, including static electricity,
- c) The facilities, substances used, processes, and their possible mutual interactions in the workplace,
ç) The magnitude of the potential explosion effect.
After identifying possible explosion scenarios, recommendations are provided by calculating the explosion intensity and pressure effects at certain distances.
Findings and Recommendations from the Explosion Protection Document
All work conducted in accordance with the “Regulation on the Protection of Workers from the Hazards of Explosive Atmospheres” and relevant standards are evaluated, and the current status of the facility is presented to the authorities in the conclusion section of the report. As a result, the deficiencies in the facility and the most suitable methods for their rectification are shared with facility authorities, creating a roadmap for the necessary actions.
For the findings and recommendations of the Explosion Protection Document to be effectively managed by facility authorities, it is crucial that the identified issues and recommendations are feasible. For example, a recommendation aimed at eliminating a release source may render certain process steps impracticable, or a recommendation to reduce process temperature to prevent exceeding the flash point may lower process efficiency.
The findings and recommendations from the Explosion Protection Document should include:
- Elimination of release sources without affecting the process,
- Improvements in ventilation efficiency to eliminate the hazardous area in cases where the release source cannot be eliminated,
- Proper selection of equipment in situations where the hazardous area cannot be eliminated.
.
ATEX Directive and Technical Articles on the Explosion Protection Document (EPD) can be explored through the following links:
Our Services
Our Trainings

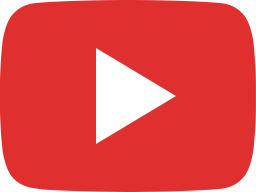
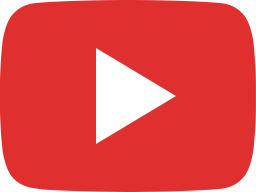
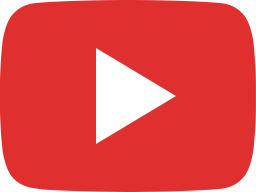
