Proses Safety Management
Is it hard to manage the changement? Is there any need for a new system? How effective is my system?
Why is the Safety Management System Important?
Process Safety Management is a set of systematic analytical methods used to control hazardous chemicals. Process Safety Management practices help companies manage process safety risks as well as increase productivity and business optimization.
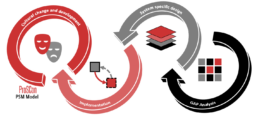
Elements of Process Safety Management
Process Safety Management can be designed in different element structures. The most important of these are listed below:
- Seveso Directive Safety Management System Model with 7 elements in force in our country,
- 14-element OSHA PSM Model,
- 20-element CCPS RBPS (Risk Based Process Safety) Model
The selection of the model that complies with the operational dynamics and compliance with the legislation is one of the most important points in Process Safety Management.
Safety Management System – SEVESO | Process Safety Management – OSHA | Risk Based Process Safety – CCPS |
Organization and Staff | Employee Engagement | Process Safety Culture |
Process Safety Competence | ||
Labor Participation | ||
Training and Performance | ||
Subcontractor Management | Subcontractor Management | |
Determination and Evaluation of Major Accidents | Process Safety Information (PSI) | Process Information Management |
Process Hazard Analysis (PHA) | Hazard Identification and Risk Analysis | |
Operational Control | Mechanical Integrity | Asset Integrity and Reliability |
Hot Work Permit | Safe Working Practices | |
Operating Procedures | Operating Procedures | |
Execution of Operations | ||
Pre-Start Safety Review (PSSR) | Operational Preparation | |
Change Management | Change Control | Change Management |
Planning for Emergencies | Emergency Planning and Response | Emergency Management |
Performance Monitoring | Event Research | Event Research |
Measurements and Metrics | ||
Review and Audit | Compliance Audits | Compliance with Standards |
Examination | ||
Management Review and Continuous Improvement | ||
– | Trade Secrets | Access to Stakeholders |

Management systems are the method of controlling the processes by regulating the application principles. The Process Safety Management System is a system developed to control the risks posed by dangerous operations such as production, storage and transportation. Directive 96/82 / EC has been made compulsory by the European Union in lower and upper level Seveso establishments. In our country, it is compulsory at lower and upper level facilities within the scope of Regulation on Prevention and Mitigation of Major Industrial Accidents published in the Official Gazette dated 30 December 2013 and numbered 28867.
Process Safety Management System should be integrated with the existing management systems of the organizations. In this way, the efficiency of the management system will be increased and adapted to the culture of the company. With this system, the elements listed below will be controlled by a management system.
- Organization and Staff
- Determination and Evaluation of Major Accidents
- Operational Control
- Change Management
- Planning for Emergencies
- Performance Monitoring
- Review and Audit
Among the elements of the Safety Management System, human errors are the most important factor that will affect the frequency of major industrial accidents. It is important to check the most frequent occurrences of human errors for the control of major industrial accident frequencies. Change management and maintenance operations are the main activities affected by human errors. Controlling the following factors will mean controlling the safety levels of the organizations as a result of process safety studies.
- Safety Culture and Quantification of Human Factors,
- Maintenance Management and Maintenance Applications Optimization,
- Change Management Applications,
- Experienced Accident Research
The effectiveness of the Safety Management System will help prevent all accidents within the company and prevent loss of resources. Integrating the process safety management system to be installed in the facilities with the other management systems implemented will mean the establishment of an integrated system away from the clumsiness by placing the whole process on the safety base. Making the safety management system established with internal and external inspections operational will bring continuous improvement.
ProSCon Process Safety Management (PSM) Projects
- Inspection and examination of the existing system,
- Establishing a business-specific roadmap by assessing the identified deficiencies and non-conformities,
- Interaction of deficiencies with other existing management systems,
- Establishment of the PSM system with the working team,
- Determining the performance indicators of the PSM System and measuring the required safety culture,
- Increasing the plant process safety culture by planning studies in accordance with the safety culture deficiencies,
- Identifying and improving the communication deficiencies of the system designed with network diagrams,
- Continuous improvement of the system through inspections.
Our Services
Our Trainings

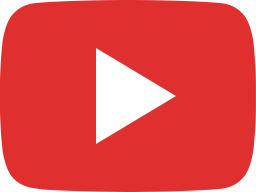
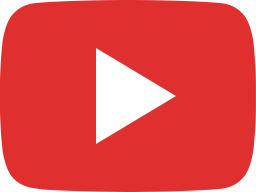
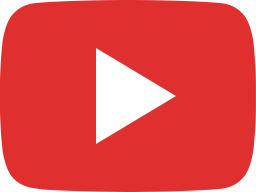
